铜是如何炼成的:一文看懂铜冶炼工艺
来源:找钢指数
2022年04月19日 20:00
专栏:铜
铜的冶炼过程是铜产业链的重要环节,了解铜的冶炼工艺对于分析企业的成本变化、生产动向、产量波动等方面都有较大的帮助。因此,本文首先从梳理铜的冶炼工艺入手,详细探讨了主流炼铜工艺,即火法炼铜的各个阶段。其次,本文对比了传统及现代冶炼技术的区别,从冶炼工艺的角度分析相应的成本差异。最后,本文简要讨论了不同炼铜阶段下,企业检修对精炼铜产量的影响变化。
铜冶炼的基本方法
铜冶炼一般是指从铜精矿到精炼铜的形成过程,主要分为火法冶炼与湿法冶炼两种技术路线。如图1、图2所示,火法冶炼以硫化铜精矿为主,通过熔炼、吹炼、火法精炼、电解精炼等环节形成电解铜,而湿法冶炼以氧化铜矿为主,通过浸出、萃取等环节形成电解铜。
两种方式各有优点,火法炼铜的优点主要是生产效率高,能耗较低,电解铜的质量较好,且可以较好地回收铜矿中的有价金属;缺点为硫化矿随着持续的开采,品位逐渐下降,选矿费用将成倍提高,同时因其需要增设控制SO2污染的环保设施,所需设备流程相对复杂,整体投资成本较高,经济效益欠佳。湿法炼铜的优点主要是不产生SO2污染,所需设备相对简单,整体投资成本较低,易于实现机械化和自动化;但其缺点为当前技术水平下原料的约束较多,既难以回收有价金属,同时其产生的硫酸亚铁溶液可能会导致环境污染(见表1)。现阶段,火法炼铜仍是主流,因此本文重点关注火法炼铜技术。
熔炼冰铜的工艺对比
火法冶炼可以粗略地分为“粗炼”和“精炼”两个环节,粗炼环节即:铜精矿——冰铜——粗铜,精炼环节即:粗铜——阳极铜——精炼铜。其中,从铜精矿到冰铜的过程是火法冶炼各种技术的主要差异所在,我们常见的一些技术术语,比如“顶吹”、“侧吹”、“闪速”等,均属于粗炼环节的各项技术。各个技术之间从流程、工艺、理念到优劣势等各个环节均有明显差异,因此这里重点对比各类熔炼工艺的区别与优劣。
1. 传统工艺
熔炼冰铜的传统工艺主要有密闭鼓风炉、反射炉和电炉。主要区别在于熔炼的主要设备、化学反应过程有差异,但本质上都是使铜精矿产生氧化反应,目前均不是主流工艺,因此不做过多介绍,可以通过表2查看更多细节。(见表2)
2. 现代工艺
传统工艺的生产效率低、烟气难以有效回收等问题推动冶炼工艺的改进,逐渐衍生出现代炼铜工艺。现代炼铜工艺主要分为熔池熔炼法和闪速熔炼法,二者均起源于上世纪70年代。
现代熔池熔炼法,有效利用富氧鼓风,将炉料直接加入鼓风搅动的熔池中迅速完成气、液、固相间反应。根据鼓入的风口位置不同,可分为侧吹、顶吹、底吹三种方式。顶吹熔池熔炼法,例如ISA法、奥斯麦特法、三菱法、顶吹旋转转炉法(TBRC),即将富氧空气从炉顶的喷枪鼓入,使熔体在翻腾中发生反应。侧吹熔池熔炼法,例如诺兰达法、瓦纽科夫法、特尼恩特法、白银法,即将富氧空气从设于侧墙的风嘴鼓入,使炉料在熔池内发生熔化、氧化反应。底吹熔池熔炼法,例如我国的水口山法,即将氧气从炉底直接鼓入熔体,从而使熔池剧烈搅动发生反应。(见图3&表3)
现代熔池熔炼法优点明显,一方面,富氧空气的股入可在短时间内促进炉料与空气快速反应,熔炼能力强大。另一方面,对原料的水分和形状要求相对较少,熔炼时的烟尘率较低,且熔池可通过分区来控制不同的氧势位。不过此方法对喷嘴、喷枪及冶金炉等设备有严格的要求,设备较易损坏意味着需要经常更换维修。
闪速熔炼法,基本原理是将预热空气和颗粒很小的干燥精矿以一定比例加入反应塔顶部的精矿喷嘴中,在喷嘴内空气和精矿发生强烈混合下,迅速以悬浮状态垂直喷入反应塔内,当炉料布满反应塔截面后立即燃烧。闪速熔炼结合了强化扩散和强化热交换两种因素,熔炼过程的生产力显著提高。闪速炉渣中Fe3O4的含量较高,渣含铜量约为1%-3%,意味着炉渣需要处理,主要依赖电炉贫化法或选矿法提铜。目前,常用的方法是奥托昆普闪速炉以及因科(INCO)闪速熔炼法。(见表4)
闪速熔炼的优点也较为明显。一是由于充分利用铜精矿的表面积,焙烧和熔炼两道工序在一次作业中完成,流程短、生产效率高。二是充分利用精矿中硫和铁的氧化热,燃料消耗较少、热效率高。三是生产的冰品品位高、脱硫率易控制,烟气中SO2浓度高可用来制酸及减少污染等。不过,该方法仍有部分缺点,一是对原料有要求,即铜精矿要充分干燥,熔剂需经粉碎;二是炉渣含铜高、烟尘率高;三是设备投资大,所需辅助设备多,因此基本为大型工厂所用。
吹炼粗铜的基本工艺
从冰铜——粗铜的过程称为吹炼粗铜,这一步是为了除去冰铜中的铁和硫及部分有害杂质,将冰铜进行吹炼后,方能得到粗铜。吹炼的基本原理是将压缩空气在有石英熔剂存在的情况下,吹过炉内熔融的冰铜,这一过程所需的热主要由吹炼过程中发生的放热反应供给,无需消耗额外的燃料或电能。一般情况下,粗铜的含铜量约为98.5%-99.5%,而炉渣成分中除了铁和二氧化硅外,含铜量较高,通常会返回熔炼炉做进一步回收处理。烟尘中的SO2同样需要收尘制酸处理。
传统意义上,企业一般使用PS转炉(卧式碱性炉衬转炉)作为吹炼设备,相应的配套设备有加熔剂设备、烟罩、传动系统、供风系统和排烟系统。至上世纪90年代,“双闪”工艺(闪速熔炼-闪速吹炼)问世后,部分大型企业逐步用此方法取代传统转炉吹炼方法。
“双闪”工艺对原料要求严格,不仅在闪速熔炼前需将铜精矿干燥(含水率控制在0.3%以内),而且在闪速吹炼炉前需将熔炼的冰铜粒化,再采用立式磨制成冰铜粉后,才可实施吹炼步骤。相对于传统冰铜的液态吹炼方式,这种工艺可将耗水量减少约75%,硫的回收率可高达99.9%。(见图4)
铜的精炼工艺
为了提升铜的使用、加工性能,需要除去粗铜中的杂质,如镍、铅、砷等,同时回收其中的有价金属,如金、银等,这便是粗铜的精炼工艺。该流程一般分为两个阶段,一是将粗铜火法精炼成阳极铜,二是将阳极铜电解精炼成电解铜。
1. 火法精炼
火法精炼是粗铜——阳极铜的过程,基本流程是在精炼炉内向粗铜熔体内鼓入空气,使熔体中对氧亲和力较大的杂质如锌、铁、铅、镍等发生氧化,以氧化物的形态浮于熔体表面形成炉渣,或挥发进入炉气而除去,残留的氧经还原脱去后,即可浇铸成阳极板。归纳来看,这一过程可分为加料、熔化、氧化、还原、浇注五个步骤。在还原步骤中,目前主流的还原剂有氨气、石油液化气和重油,其中我国以重油为主,吨铜约需4kg还原剂。
精炼炉一般有固定式精炼反射炉、回转式精炼炉以及倾动式精炼炉,其中,回转式精炼炉的精炼效果较好,产品质量较高、节能且生产成本较低,具有良好的经济效益。
精炼后的产物除了阳极板(含Cu量99.2%-99.7%)外,还有炉渣、炉气和烟尘。其中,炉渣的含铜量较高,约为10%-30%,一般需要将其返回转炉吹炼或加入鼓风炉做进一步处理。炉气中的成分一般为O2、CO2、CO,不含SO2,所以可将其直接排出。
2. 电解精炼
电解精炼是阳极铜——精炼铜的过程,基本流程是在电解槽中将阳极板和始极片(纯铜或不锈钢)同时浸入电解液(硫酸和硫酸铜的水溶液),在直流电的作用下,阳极上的铜以离子状态进入电解液并在阴极上电化析出,成为阴极铜(电解铜),有价金属以阳极泥的形式沉淀回收。此方法的基本原理是利用了铜和杂质的电位序不同来分离二者。
传统电解工艺中,阴极始极片主要使用纯铜片制作,此工艺相对复杂且需要独立的生产系统,劳动强度大,生产过程中需要定期更换始极片而提升成本。上世纪70年代后,永久性不锈钢阴极法投入使用,即阴极采用不锈钢始极片,阴极铜由自动剥片机从不锈钢阴极上剥取。这种方法不仅无需建立单独的始极片生产车间,而且可大大减少更换始极片的周期,从而降低生产及劳动力成本。目前来看,这种方法得到了国内外冶炼厂的广泛使用。永久性不锈钢阴极法又可分为ISA法、KIDD法及OT法,基本形式一样,细节有些许不同。(见表7)
铜冶炼工艺的成本组成
了解铜的冶炼工艺后,这里我们基于火法炼铜流程,简单讨论一下冶炼过程中的成本构成。铜冶炼成本主要分为五个部分,分别是熔炼成本、电解成本、烟气制酸成本、渣选矿成本及阳极泥处理成本。
熔炼成本主要包含熔炼、吹炼及火法精炼的三个流程中所涉及的原材料成本、辅助材料成本、燃料及动力成本、生产人员薪酬及制造费用。其中,原材料成本即铜精矿中的含铜价格,变动较大,应重点关注。铜精矿含铜价格可分为进口铜精矿含铜价格和国产铜精矿含铜价格。其中前者根据铜精矿品位、基准铜价、TC/RC、扣减率和汇率的变化而波动;后者根据铜精矿品位、基准铜价取不同的计价系数及价差而定。
电解成本中包含电解精炼及电解液净化的两个流程中所涉及的各类成本,但不涉及原材料成本。因电解工艺中包含传统电解法和永久性不锈钢阴极电解法,这里我们基于《云铜传统电解与ISA电解完全成本对比分析》一文中所提及的数据,对比两种电解方法下的成本差异(见表10)。表中数据是基于云铜某车间生产18万吨阴极铜所需的相关成本,可以看出两种工艺的完全成本相差不大,ISA电解法的完全成本较传统电解法高4元/吨铜,主要成本差异集中于基建投资费用。不过,该分析未考虑传统电解的阴极周期替换成本以及ISA电解法中劳动力的减少和流程的简化所带来的机会成本。因此,相对于传统电解法,ISA电解法的相关成本、技术经济指标等将更胜一筹。需要补充的是,电解成本中还应考虑硫酸消耗所带来的额外成本。
烟气制酸成本主要针对于烟气中SO2浓度较高时回收制酸时所需的加工成本及尾气脱硫成本。SO2鼓风机通常占整个硫酸电耗的70%,而SO2浓度与烟气量成反比,因此烟气浓度升高有助于降低单位硫酸产品的电耗。同时,回收的余热可计价扣减硫酸生产成本。
渣选矿成本应考虑炉渣来源,因其配以不同种类、不同用量的辅助材料,所以渣选矿成本应根据不同企业的冶炼工艺分别计算。
阳极泥处理成本中波动较大的为铜精矿中金、银的计价。同含铜计价方式一样,分进口及国产两种类比,此处不再赘述。
综合上述的五类成本及前文所述的冶炼工艺,我们基于《铜冶炼成本计算需关注的问题》一文中的数据,对比不同冶炼工艺下的成本差异。
因表中数据搜集的时间段不同,原料的加工费及汇率均有差异,对各项目间单位成本产生一定影响。不过,总结以下三点:①项目1的地理条件使其电价、燃料价及劳动成本较低,导致阴极铜生产成本较低,实际生产过程中,相较于转炉吹炼,闪速吹炼的能耗较低,建设运营费用较低,因此相同条件下单位加工成本较低;②对比项目3和项目4,精炼铜的加工成本会随冶炼工艺中配套设备的增加而增加;③对比项目2和项目3,在其他条件不变的情况下,企业生产规模化后会使其边际成本下降,从而降低精炼铜加工成本。
对我国冶炼厂二季度检修的思考
熟悉了解铜冶炼的基本工艺对于我们判断冶炼厂的产量具有较大帮助。以冶炼厂检修为例,对于精炼环节与粗炼环节的检修,所产生的实际影响是不同的。根据SMM及我们调研情况,表12为今年二季度有检修计划的冶炼厂及其相应冶炼工艺。
表中显示,除了大冶有色是6天的小型检修以外,其余各厂基本均为30天(或以上)的相对大型检修。据了解,一般来说检修时长在20天以内的为精炼阶段的检修,超过20天的通常是粗炼与精炼阶段共同检修。对于粗炼阶段检修,若冶炼厂可正常外购粗铜或阳极铜,则精铜产量并无较大影响。对于电解精炼阶段检修,若冶炼厂有闲置电解槽则精通产量同样不受影响,反之,则短期精铜产量将会受到一定影响。
然而,电解精炼检修对产量的具体影响仍需分情况考虑,一般分为大检修和小检修。正常情况下,企业大检修每三年一次,对精炼铜的产量会产生相对明显的影响。小检修通常指对电解槽的检修,其对精炼铜产量的影响并不能简单以企业年产量÷365天×检修天数来考虑,因为企业电解车间内设有若干个电解槽,一般采取分批检修的方式进行。举例来说,若企业分三批对电解槽进行检修,则对精炼铜产量的影响应以企业年产量÷365天×检修天数×1/3来计算。
因此,企业检修对产量的影响究竟如何,应结合其生产方式、冶炼工艺、检修习惯、外部因素等方面综合考虑,从而做出相对准确的判断。
总结
综上,铜冶炼工艺大致可分为火法炼铜及湿法炼铜两类,八成以上的精炼铜来源于火法炼铜工艺。火法炼铜主要分为三阶段:铜精矿先熔炼成冰铜、再吹炼成粗铜、最终精炼成电解铜。企业主要的冶炼技术差异集中于熔炼冰铜的阶段,传统与现代的熔炼工艺区别较大。现代冶炼技术中,冶炼成本主要分为熔炼成本、电解成本、烟气制酸成本、渣选矿成本及阳极泥处理成本五个部分,不同的冶炼工艺具有一定的成本差异。另外,企业检修对精炼铜产量的影响也需要结合企业的生产方式、冶炼工艺、检修习惯等多方面综合判断。
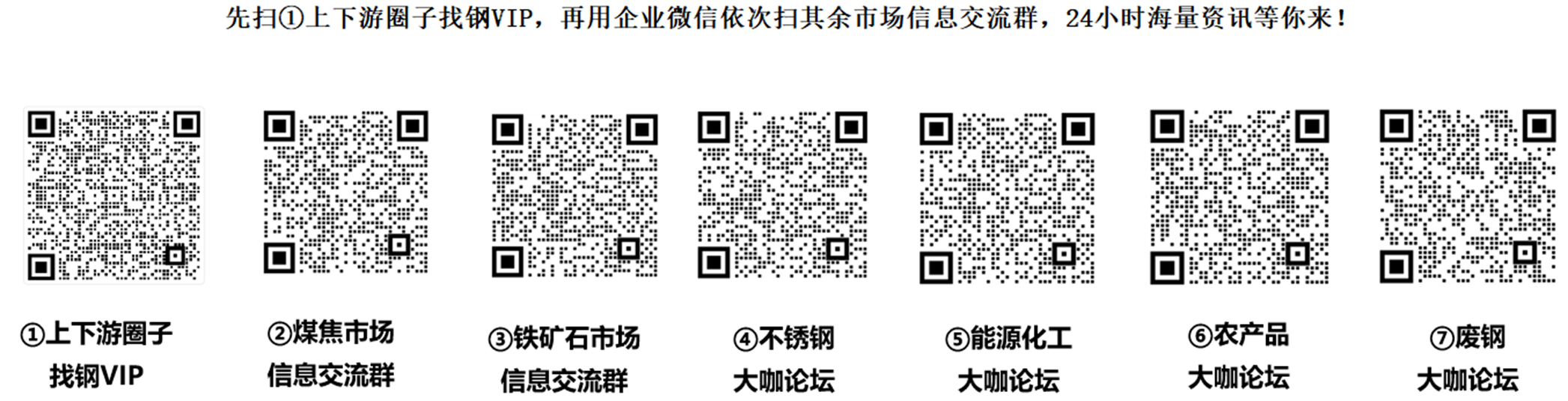
资讯编辑: 思域
资讯监督/投诉:福克斯 021-60100586-9
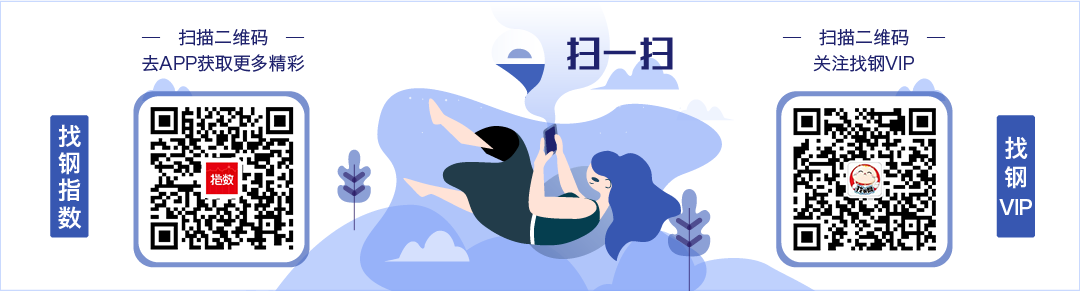